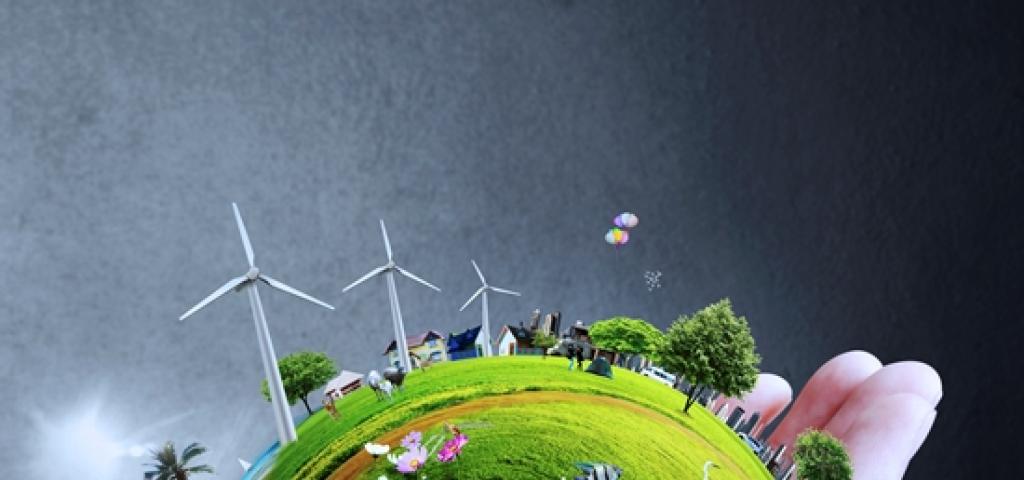
Predictive Maintenance and Adaptive Analytics Raise IoT Value
One of the most intriguing aspects about the Internet of Things (IoT) is that it can positively impact such a wide range of markets, including industrial, energy, health care, and others. In his thoughtful and rich blog post below, guest blogger Alexander Damisch, Senior Director, IoT Solutions, Wind River, explores how the predictive maintenance and adaptive analytics capabilities of IoT can add measurable value for businesses.
The Internet of Things (IoT) will be fundamental to creating new services and revenue streams, and enhancing productivity and efficiency in existing infrastructure by delivering intelligent and autonomous decision-making in real time. But it also raises questions, including: How can IoT help businesses reduce operating expenditures (OPEX), generate new revenues, and enable innovation?
A key use case for IoT is predictive maintenance: the ability to accurately diagnose and prevent failures in real time is a major advantage for companies and is vital for critical infrastructure applications. A failure of high-tech machinery and equipment can prove to be highly expensive in terms of repair costs, in addition to lost productivity from the resulting downtime. Typically, technicians have been sent to carry out routine diagnostic inspections and preventive maintenance according to fixed schedules, which can be a costly and labor-intensive process with little assurance that failure will not occur between inspections.
One example in the renewable energy sector is a wind farm—and in the extreme case, an offshore farm. Wind turbine systems contain a great deal of technology, including a generator, a gearbox, and a multitude of electronics, including control systems to adjust blade pitch and so on. If any element fails—due to dust buildup or cumulative vibrations, for example—the remote location means the repair cost will be extremely high. In addition, given that weather will always be a significant factor in this particular example, a turbine may not be producing electricity for some time.
However, on-site sensor-equipped systems can collect data from multiple turbines, not just a single turbine, enabling failure analysis to be performed to predict when a system or component is likely to malfunction due to stress or overheating, and thereby enabling better operator or autonomous decisionmaking for maintenance. For example, if there is a high likelihood of the gearbox breaking down within a turbine, then switching to a lower performance mode and a reduced mechanical load, while still delivering 80 percent efficiency, could mean continued operation and further electricity generation for several weeks. This would allow scheduled maintenance that combines the repair and maintenance of more than just one turbine.
A second important use case is adaptive analytics, which involves looking at an overall system or a system of systems. Based on much of the same data already being collected for predictive maintenance, adaptive analytics enables equipment and devices to analyze enormous amounts of data and make real-time decisions to help refine and improve operational processes.
Revisiting the wind farm as an example of adaptive analytics, the first turbine in a row of turbines will usually run at optimum performance. However, this first turbine will create turbulence, which is likely to have an impact on the operational efficiency of its nearest neighbor. So setting the same blade pitch for all the turbines according to the wind speed is unlikely to achieve optimum performance for the wind farm overall. But information from the first turbine, such as blade pitch and rotation speed, can be used to adjust the parameters of the second, and so on, enabling the overall operation to achieve close to optimum performance. And this improvement is enabled just by tuning various parameters, without any need to install further hardware to improve operational efficiencies or reduce wear.
The adaptive analytics and predictive maintenance capabilities of IoT play a significant role in providing opportunities for new revenue streams, and not just reducing OPEX. In industrial markets, for example, historically the big players have had two main ways of generating revenue: the traditional way of selling devices such as control systems or motor drives or human–machine interfaces (HMIs); and complete hardware and software system solutions including maintenance service level agreements (SLAs). But both of these business models are under intense pressure from a cost point of view, with increasingly strong competition and significantly reduced margins—especially after the recent financial crisis, which has meant oversaturation in the market for manufacturing equipment.
In the case of major industrial and automotive equipment OEMs, they have a huge base of already installed equipment on-site at customer premises—which can be a challenging situation for innovation. However, in addition to new products or assets, one way to increase revenue is to obtain new, recurring revenue streams based on existing and already deployed devices. The ability to innovate and deploy simple solutions that allow the connection of equipment to IoT with the help of solutions like Intel Gateway Solutions for IoT, can provide customers with significantly reduced operational costs and additional value via predictive maintenance and adaptive analytics. A service fee could be based on production volume, number of deployed devices, or a certain amount of data. This could give rise to a subscription-based business model including the leasing of equipment with ownership retained by the device manufacturer.
The possibilities offered by IoT are many and should be embraced by businesses operating in many different markets, including industrial automation, networking, health care, energy generation, and transportation, among others. Predictive maintenance and adaptive analytics can significantly help companies increase operational efficiencies and reduce OPEX, and also deliver potential new streams of revenue for major players based on already deployed assets.
Post originally published on IoT@Intel.