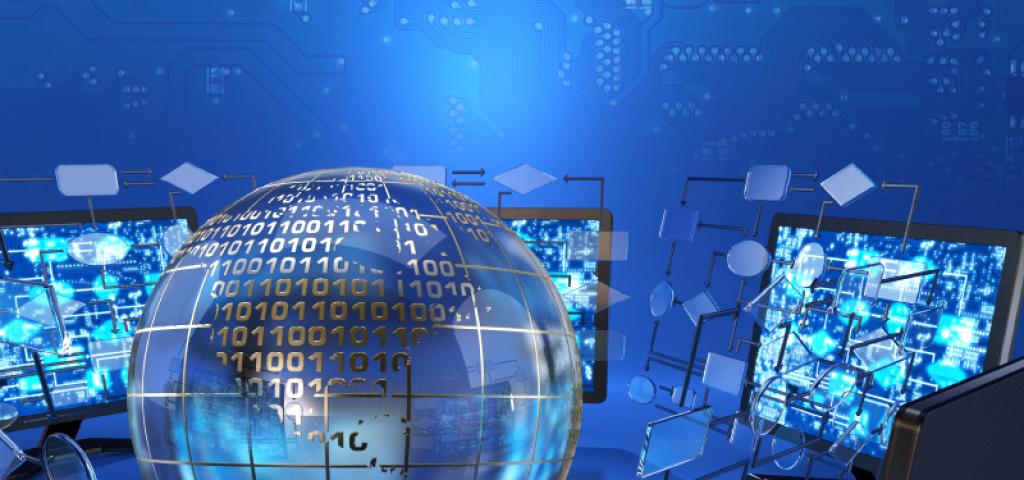
The Internet of Things and Manufacturing: How to Stay Competitive in a Rapidly Changing Market

Not so long ago, the manufacturing world was divided in two. The high labor cost countries, which formed the target market for most products, did the research and development, while the lower wage countries were the production workbench. This arrangement was not purely good or bad. It created a lot of jobs in what were then less developed countries and helped them grow economically. It also helped produce high-tech gadgets at reasonable prices that generated extremely high revenues for leading companies headquartered in high labor cost countries.
Today, things are a bit more complicated. Many former cheap labor countries are not that cheap anymore, and no longer considered underdeveloped. They caught up in the fast lane, and in some instances even overtook the former industrial leaders. Witness the “solargate” debacle in the US, in which outsourcing full production of solar panels to Asia meant also outsourcing the process knowhow, which displaced the US solar industry. Once expertise is outsourced, it raises the risk that innovation will be transferred from the originating to the producing country.
Many tech industry leaders, including former Intel chairman Andy Grove, have commented on this phenomenon. There is a movement afoot, along with the political will, to “move manufacturing jobs back to the US,” or any other high-cost country. This comes in part from the fear of losing control over innovation, with the argument that high-tech production can compensate for the higher labor costs in countries such as the US or Germany.
This trend is slowly but steadily leading to manufacturing investment moving back to the “OEM” country. Apple is now producing Gorilla Glass screens and the Samsung-produced CPUs in the US, and has started assembling its more expensive units in North or South America, much closer to the company’s home base.
The Internet of Things (IoT) is accelerating the trend of moving factory floor jobs into the back office in order to stay competitive, improve quality and reduce the environmental impact of production. This was well explained in an article in The Economist, April 21st 2012, “The Third Industrial Revolution.” Manufacturers now need to rethink and change from the way they produced in the past.
With a huge installed base, the biggest challenge involves connecting existing infrastructure to decision-making processes without compromising security, and without incurring the enormous cost of rebuilding the whole infrastructure. Wind River’s strategy for brownfield allows for retrofitting secure connected intelligence to the installed base today, while our forward-looking capability for “function virtualization” enables the consolidation of systems and functions into more efficiently developed and maintained systems of systems. With this approach, we are not only providing immediate pain relief for today’s challenge, but also setting the roadmap for future system consolidation and the path into the cloud.
Manufacturers need to think of the IoT not merely in terms of technology, but rather in terms of the business case. How can the IoT help you be more competitive or produce with higher quality, lower cost and less environmental impact? The payoff will be to stay relevant in the global manufacturing market that is disrupted by geopolitical change and pressure to “digitize” manufacturing. IoT solutions will keep you competitive in a rapidly evolving manufacturing market today and in the future.