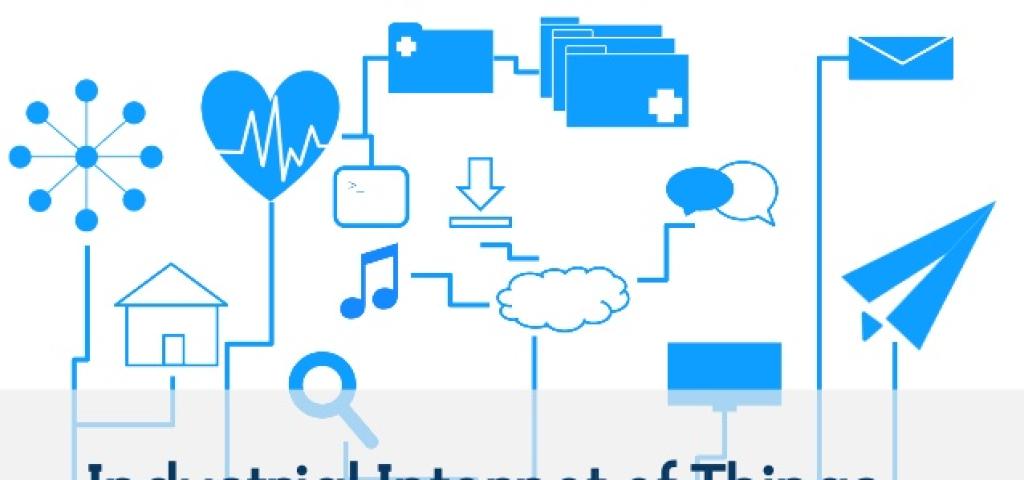
Time Sensitive Networks and IIoT

The Internet of Things (IoT) is all about data, getting access to data, understanding that data and then using that data to act. The Industrial Internet of Things (IIoT) is no different, it extends the IoT into devices that control many of the items that make our lives comfortable. Power plants, water processing plants, wind farms, manufacturing lines, robots that build cars, cell phones and many other devices that we use daily.
These control devices generate lots of data, data about performance, oil temperature, friction in bearings, vibrations, tool offsets, error conditions and so forth. All this data is valuable as it provides information about the operation of the devices. Crunching that data is important as it allows early detections of things that are wrong, or may go wrong soon.
If a robot measures that it’s tool positioning is slightly off, then this could be a problem with the tool, the product that is being worked on, the manufacturing line itself and so forth. Being able to catch these conditions prevents the error from propagating, prevents re-work and prevents faulty product from reaching the end customer.
If a certain process in a water processing plant is measuring higher or lower flow all of sudden, then this could be because a valve is stuck, a filter is dirty, or certain other stages in the pipeline need to be adjusted.
The driver is always the same. Catching these conditions early at the source prevents the error from propagating and saves cost. There is a great infographic by General Electric about the power of 1%. How much money could we save if we can make industries 1% more efficient?
So, data is important. Data-crunching is typically done in the cloud, looking at historical data and data collected from hundreds or thousand of similar devices. This data is not typically real-time sensitive, so it can be sent in a best-effort way. However, with Industrial control devices, real-time is important too. We need to be able to control devices in real-time and we need them to be able to transmit data about their performance.
Much device control happens locally today. A robot has a local control node that reads sensors and drives actuators. However, if we have 2 robots that are collaborating, or if we have a human interacting with a robot, then we need to be able to control these devices from a larger distance, either by some type of server on-premise, or possibly even further away. There are a lot of savings that can be gained by controlling a manufacturing line not from the local control nodes, but from a real-time data center somewhere on the factory floor. That control data needs to be absolutely guaranteed real-time with jitter in the low microsecond range. On top of that, these devices need to be small and affordable, which means that we need to do this data collection and control over a single wire.
This pattern is not new. This type of consolidation of function has happened in the IT industry with virtualization and is happening now in the networking industry with Network Functional Virtualization (NFV) and will happen as well in industrial devices with Device Function Virtualization (DFV).
As mentioned, for this consolidation (Device Function Virtualization) to work, we need to be able to combine general purpose data and low jitter real-time control on a single wire, and this is exactly where Time Sensitive Networking (TSN) comes in. TSN is described in the IEEE 802 standard and it is an open platform that allows real-time control data to be transmitted and sent over the same network connection as general purpose data. TSN builds on the learnings gathered with other, more proprietary, protocols such as EtherCAT, ProfiNET and others. The goal of TSN is to provide an open platform that many companies build upon that can deliver micro-second level worst case jitter between devices from multiple vendors.
To prove that this is indeed possible, the Industrial Internet Consortium is collaborating to build a testbed that contains devices from multiple vendors: National Instruments, Bosch Rexroth, Cisco, Intel, Kuka Robotics, Schneider Electric and TTTech. Wind River has been working on TSN support as part of it’s safe and secure VxWorks real-time operating system and, hence, VxWorks is used for the real-time nodes in this testbed. More information about the testbed and the participants can be found here.
TSN support in VxWorks provides access to global time that all participants can agree on, as well as hardware features that allow the processor and networking devices to correlate local time and global time, and then to utilize that time in the sending and receiving of packets.