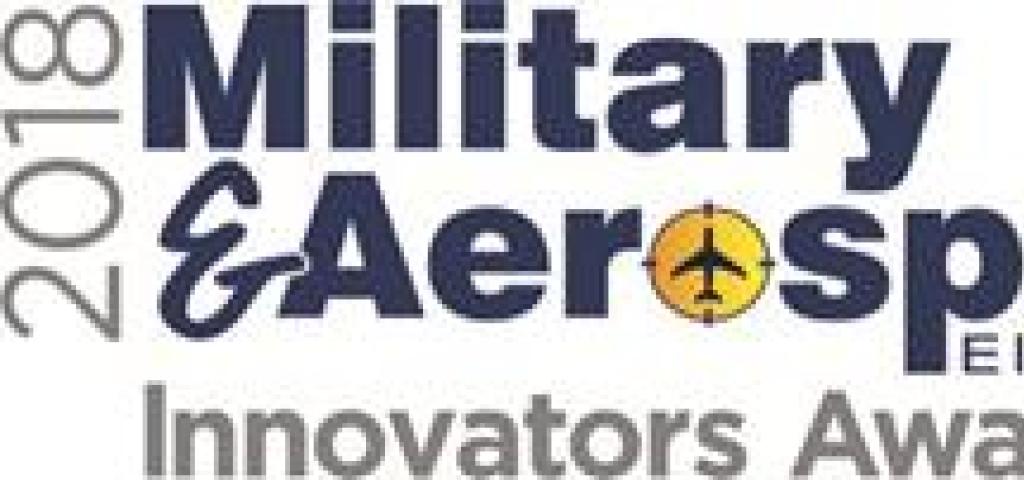
Wind River Simics Recognized with Top Innovation Award

Wind River has been selected for the third time in a row as a platinum honoree by Military & Aerospace Electronics Magazine. This year, the technology innovation award goes to Wind River Simics, a full system simulator that solves significant DevOps challenges in today’s manufacturing processes. Wind River won this distinction in previous years as well, with VxWorks 653 and the revolutionary work done together with partners such as Presagis and CoreAVI, which included VxWorks.
A Celebration of Technology
This is the highest ranking of Military & Aerospace Electronics’ 2018 Technology Innovation Awards. Products entered in this prestigious program are judged by a panel of independent industry judges. Entries are evaluated on their engineering, design qualities, and how the innovation of the product makes an impact on customer’s problems. Products chosen as Military & Aerospace Electronics Technology Innovation honorees reflect innovative design and engineering in some of the most cutting edge tech products and services in the Aerospace and Defense market.
Design Challenge
Because of their complexity and stringent safety requirements, most aerospace projects take many years to come to fruition. The rising development and maintenance costs, but also the access and availability of the system components, are the key business challenge faced by the aerospace vendors. When supporting projects built with traditional hardware-based development, testing and verification is often not practical because of the cost of supporting and maintaining the hardware. Too much time and effort would be expended trying to find old boards that are no longer available in order to run tests. Then there’s the cost of storing inventory and the issues surrounding portability. It’s difficult to replicate hardware for multiple uses. For these reasons, software simulations and digital twins have recently become essential to the aerospace programs test and verification processes and agile development of flight software.
In order to understand the behavior of the real-world system in its operational environment, developers use digital twins to debug problems and predict future problems before they happen. These digital representations are provided with inputs or stimuli that have been measured, logged, or observed in real-world systems.
How Simics Fits In
It is very common in the aerospace industry to use both physical and digital models to understand and resolve issues for missions in flight. Simics simulates frequently used aerospace processors, enabling target software to run on the virtual platform the same way it does on physical hardware. Along with Simics’ capabilities of scripting, debugging, inspection and fault injection, it enables developers to define, develop and integrate their systems using digital twins and eliminating the constraints of physical target hardware. Simics can simulate an entire system, or a system of systems, and can simulate them running unmodified software binaries identical to those that run in the physical system.
Simics is an excellent choice for seeing the unmodified software run on system controllers. Connecting Simics virtual platforms to simulation models of physical systems is a common practice. It helps many aerospace companies build twins that go all the way from large-scale system physical modeling to the actual control software—including running multiple control systems as on the control side.
Simics helps aerospace developers free themselves from the limits of physical hardware to perform software development, target environment testing, closed loop testing or validation and verification in an agile and automated way.
Simics allowed NASA’s ITC team to simulate their target hardware, ranging from a single processor to large, complex, and connected electronic systems, and build its GO-SIM product with all the desired features.
For more information on Simics visit: http://www.windriver.com/products/simics/