What Is a Digital Twin?
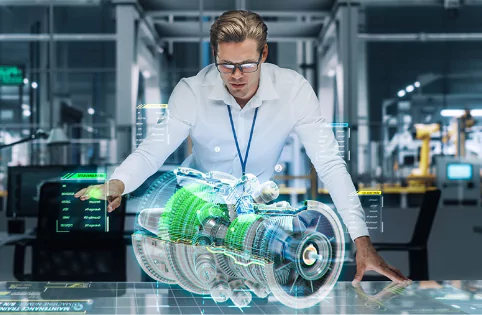
More than static models, digital twins synchronize real-time data from their physical counterparts.
A digital twin is, as its name suggests, a virtual representation or replica of something in the physical world — an entity, system, or process. It goes beyond a static model or a computer-aided design (CAD) rendering by integrating real-time data from its physical counterpart. Digital twins use sensors, connected devices, data analytics, and other technologies to capture and synchronize information about the behavior, characteristics, and performance of the physical entity they are representing. This synchronized data allows the digital twin to mirror the real-world entity dynamically and continuously.
The digital twin concept revolves around creating a digital counterpart that can mimic and simulate the behavior of its physical twin. It forms a bridge between the physical and virtual realms, enabling teams to gain insights, make informed decisions, and optimize performance. With real-time data analysis and application of advanced algorithms, digital twins offer a comprehensive and detailed understanding of the physical entity’s current state and its potential future behavior. Digital twins are useful in manufacturing, healthcare, transportation, energy, and more. They empower organizations to optimize operations, improve efficiency, reduce costs, and enhance decision-making. Leveraging the ability to simulate scenarios, predict outcomes, and facilitate predictive maintenance, teams that use digital twins can enact proactive strategies and help their organizations keep ahead in an increasingly complex and interconnected world.
Hi-Fi vs. Lo-Fi Twins
There are two key categories of digital twins, each offering distinct advantages and limitations:
- Hi-fi digital twins: Highly detailed and sophisticated replicas of their physical counterparts, hi-fi digital twins capture the smallest nuances and intricacies of the real-world object or system they represent. They incorporate advanced technologies such as high-resolution sensors, data analytics, and machine learning algorithms to gather and process vast amounts of data. As a result, they provide a comprehensive and accurate representation of the physical entity, enabling precise simulations, predictive analysis, and optimization.
- Low-fi digital twins: Simpler and less resource-intensive versions of their hi-fi counterparts, low-fi digital twins focus on capturing the essential elements and behavior of the physical object or system, rather than aiming for a high level of detail. They often use limited data sources, simplified models, and basic algorithms to represent the most critical characteristics and performance parameters. While they may not offer the same level of fidelity as hi-fi twins, they are more lightweight and easier to develop, and they require fewer computational resources.
The main differences between hi-fi and low-fi digital twins lie in their levels of complexity, fidelity, and applicability. Hi-fi twins are well suited for scenarios that demand precise analysis, simulation, and optimization, such as complex manufacturing processes or intricate infrastructure systems. They enable predictive maintenance and real-time decision-making. However, hi-fi twins can be computationally intensive, require substantial data input, and involve higher development costs.
Low-fi twins are ideal for situations in which the priorities are simplicity, scalability, and cost-effectiveness. They are suitable for applications such as basic condition monitoring, early fault detection, or preliminary system analysis. They can be developed quickly and integrated into existing systems easily, and they provide a good starting point for further refinement. While they may lack the intricate detail and accuracy of hi-fi twins, they nonetheless offer valuable insights and benefits, especially when resources or computational power are limited.
Ultimately, the choice between hi-fi and low-fi digital twins depends on the specific needs, objectives, and constraints of the application. It is essential to consider factors such as the desired level of accuracy, available data sources, computational resources, development time, and cost to determine which type of digital twin is most suitable for a particular use case.
Benefits and Challenges
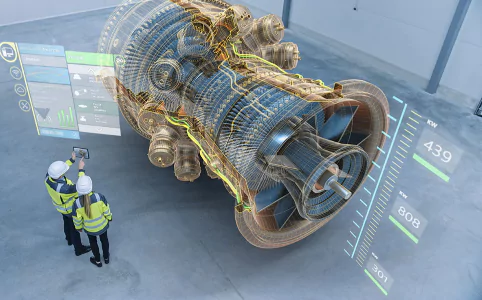
Organizations that invest in the necessary infrastructure and resources can realize efficiencies and optimization through the use of digital twins.
The adoption of digital twins offers numerous benefits to organizations, including:
- Enhanced efficiency: Digital twins enable real-time monitoring, predictive maintenance, and performance optimization, resulting in improved efficiency and reduced downtime.
- Cost savings: By identifying potential problems and inefficiencies early on, digital twins help organizations minimize operational costs, optimize resources, and reduce maintenance expenses.
- Improved decision-making: Digital twins provide a holistic view of complex systems, allowing organizations to make informed decisions based on accurate and up-to-date information.
- Innovation and optimization: Digital twins enable the development and testing of new products, processes, and strategies, minimizing risk and supporting continuous improvement.
However, the adoption of digital twins also comes with challenges, such as ensuring data security, integrating diverse data sources, and managing the complexity of the models. Organizations must invest in robust infrastructure, data analytics capabilities, and expertise to fully leverage the potential of digital twins.
Applications Across Industries
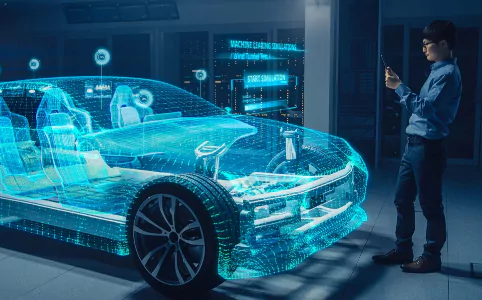
Auto manufacturers use digital twins to improve safety, optimize fuel consumption, and even analyze traffic patterns.
A wide range of industries have found applications for digital twins. Sectors taking transformative advantage include:
- Manufacturing: With digital twins creating virtual replicas of their production systems, manufacturers can optimize efficiency, predict maintenance needs, and improve overall productivity. By simulating different likely or possible scenarios, organizations are identifying bottlenecks, optimizing workflows, and improving supply chain management.
- Healthcare: Because digital twins can replicate human organs or entire bodies, they support personalized medicine and more accurate diagnoses. They improve the development of precise treatment plans and enable surgical simulations and continuous monitoring of patient health.
- Transportation: Digital twins are revolutionizing transportation systems, from vehicles to infrastructure. By creating digital replicas of vehicles and monitoring their performance in real time, manufacturers and fleet operators can enhance safety, optimize fuel consumption, and improve maintenance practices. Digital twins also assist in simulating traffic patterns and analyzing transportation infrastructure for smarter urban planning.
- Energy and utilities: Valuable insights into power grids, renewable energy sources, and oil and gas infrastructure come from digital twins. By using them to continuously monitor and analyze data, teams can predict maintenance needs and optimize energy generation and distribution.
What Types of Projects Could a Digital Twin Support?
Digital twins can provide substantial benefits to many types of projects, including:
- Infrastructure development: Whether the project goal is a smart city, a transportation network, or a utility system, digital twins allow stakeholders to visualize and simulate the impact of different design choices, optimize resource allocation, and identify potential risks or bottlenecks. The technology supports effective project management, improves collaboration across teams, and enhances overall project efficiency.
- Manufacturing and product development: Virtual replicas of factories, equipment, and products enable manufacturers to optimize production workflows, simulating and testing different production scenarios. By using real-time data from sensors embedded in machines, digital twins can predict maintenance needs and reduce downtime.
- Building and facility management: From the initial design phase to ongoing operation, digital twins help monitor energy usage, optimize HVAC systems, track occupancy patterns, and ensure compliance with safety regulations. Architects, engineers, and facility managers use them to enable proactive maintenance, help plan the use of the physical space, and enhance the comfort and well-being of the occupants.
- Healthcare and medical treatment: Digital twins can be virtual replicas of patients, organs, or even entire healthcare systems. Medical professionals can use them to personalize treatments and optimize medication dosages, enable continuous monitoring of patients’ health, detect anomalies early, and deliver timely interventions.
- Environmental monitoring and resource management: By integrating real-time data from sensors and environmental monitoring devices, digital twins can simulate and predict the impact of interventions or policy changes. They help teams optimize allocation of resources and mitigate the environmental footprint of industries and urban areas.
How Can Wind River Help?
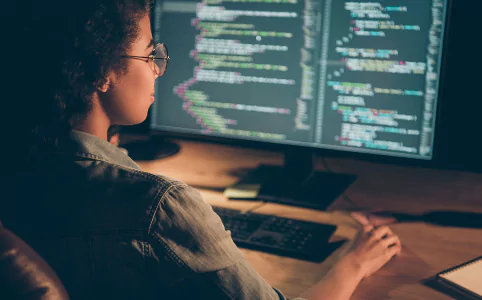
Simics gives developers on-demand access to any system, allowing a wide range of development and analytic capabilities.
Wind River Simics
Wind River® Simics® allows developers to have on-demand access to any target system at any time. It enables more efficient collaboration between developers and quality assurance teams.
Simics provides an automation API, enabling organizations to reap the business benefits of DevOps and continuous development practices to create and deliver better, more secure software, faster — even for complex, embedded, connected, and large IoT systems.
Simics also supports the Device Modeling Language (DML), open source technology that provides a powerful modeling language for simulation models.
Key Simics capabilities:
- Immediately run a simulation of popular target architectures using the built-in Quick Start Platforms for Arm®, Intel®, and PowerPC® that come with Simics.
- Simulate the target system, including processors, devices, full boards, and systems.
- Run the same software on Simics that runs on the physical target.
- Enable everyone with access to the virtual system — within teams, across teams, and with partners and the entire ecosystem.
- Analyze and debug the full system as a unit, not just as a single board.
- Debug efficiently by running the simulation forward or in reverse.
- Share system state, execution history, and virtual hardware setups with anyone, anywhere.
- Resume execution from the exact point at which it was last saved.
- Inject faults to test system robustness and diagnostic software.
- Automate manual steps and repetitive tasks with full scripting capability.
- Integrate with the existing software development environment and automated workflows, or have Wind River Professional Services do it for you.
- Integrate physics and environment simulators to build complete system simulations, or have Wind River Professional Services do it for you.
- Use the Simics Eclipse-based, C/C++ source code debugger, or use your standard software toolset.
- Use a prepackaged virtual platform from Wind River, build your own, or have Wind River Professional Services build one for you.
Wind River Studio
Wind River Studio is the first cloud-native platform for the development, deployment, operations, and servicing of mission-critical intelligent edge systems. Studio Virtual Lab allows developers to untether themselves from a one-to-one connection to a physical board. Physical hardware assets can be centralized and accessible to developers working in different time zones or on different projects. The target orchestration and registration manager simplifies the process of identifying, reserving, and attaching to a shared physical device that developers can use to test, debug, or deploy their software.
Integration with Studio allows you to create, build, run, and debug applications in Virtual Lab or on local QEMU and hardware targets. QEMU is an open source machine technology that emulates the machine’s processor through dynamic binary translation and provides a set of different hardware and device models. It can be used for application development and as a testing platform from the Studio UI, from Visual Studio, and from a command-line interface.