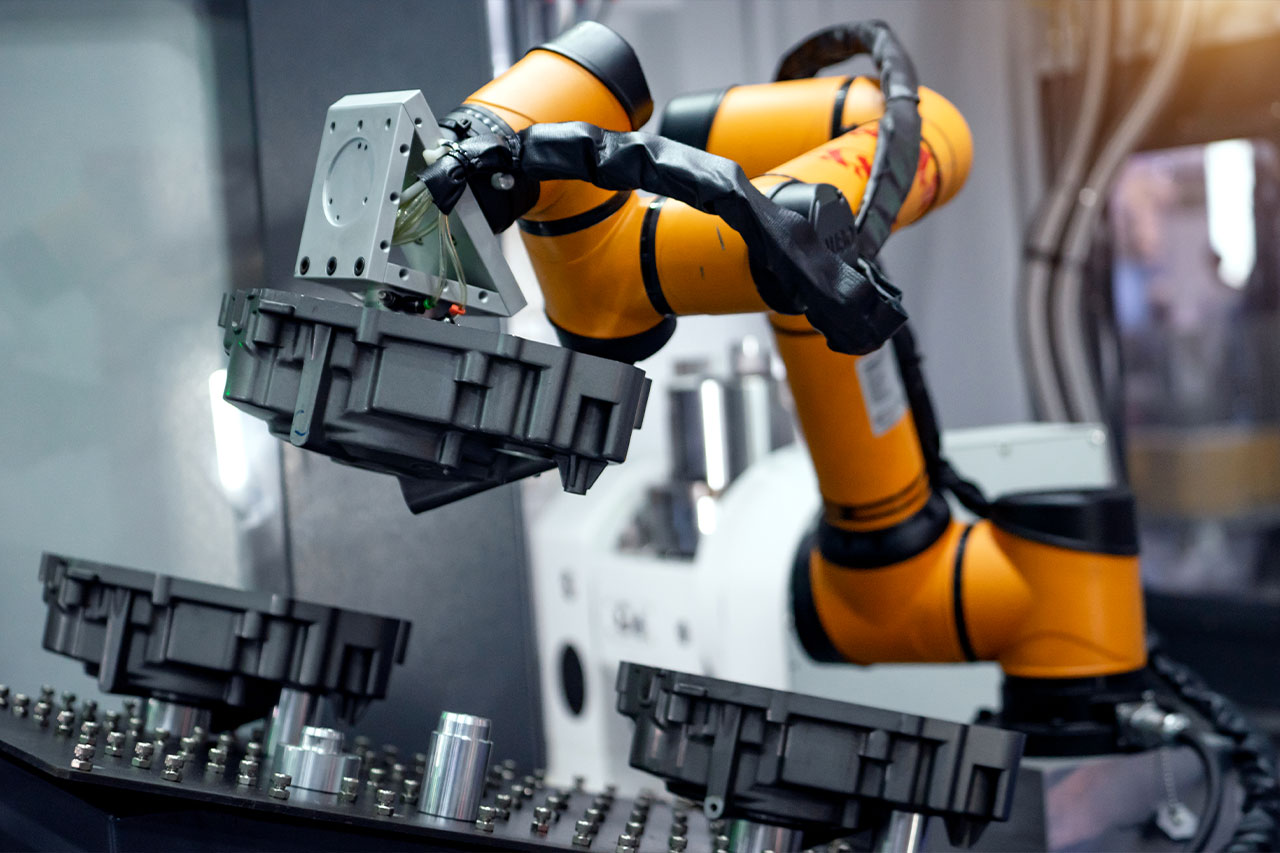
RTOS-based applications are at the core of the following cutting-edge initiatives
Pervasive AI
The acceleration of pervasive AI is made possible through a confluence of trends — open source software, cloud computing, and more sophisticated system architectures, including hardware elements such as GPU and FPGA processors — and will bring new capabilities to systems that require an RTOS to execute in an optimal way. Today’s new generation of RTOSes make it possible to pack a wide range of functions within constrained devices employed for their speed and responsiveness in industrial, retail, and healthcare settings.
RTOS-based applications at the core of pervasive AI are being brought about “by a proliferation of AI-powered smart devices able to recognize and react to sights, sounds, and other patterns. Increasingly, machines will learn from experiences, adapt to changing situations, and predict outcomes,” according to a report from Deloitte. “Some will infer users’ needs and desires and even collaborate with other devices by exchanging information, distributing tasks, and coordinating their actions. With AI embedded, rather than confined solely to the cloud, the intelligence in these devices will not depend on internet connectivity.”6
Local hardware accelerators are also helping to support AI running within edge devices. Since AI consumes large amounts of compute resources, hardware accelerators such as general processing units (GPUs) or neural processing units (NPUs) will support AI processing within edge devices. Local hardware acceleration is “one of the most exciting architectural developments that’s going on within RTOS environments,” says Koning. “You can leverage an NPU or GPU to accelerate AI algorithms and get the data into those accelerators.” Deploying an RTOS on this powerful hardware provides a “high-speed interconnect with a real-time environment that may be performing a control function,” he illustrates. Examples of applications that benefit from these features may include object detection, anomaly detection, or neural network learning algorithms.
The advantage these edge devices and systems bring is their rapid response times. “They will not suffer the latency entailed by transmitting data to the cloud for analysis,” according to Deloitte. “Lower latency and connectivity independence will enable all kinds of applications — such as vehicle navigation and some healthcare applications — that require instantaneous response and robust performance even when connectivity is poor.”
IoT
Intelligence at the edge is built on high levels of connectivity and interaction among devices, sensors, and systems across networks. The emergence and projected growth of 5G networks has accentuated the ability of devices to respond in real time to events or commands.
An essential component of pervasive AI, the Internet of Things (IoT), has become a priority in RTOS deployments. For example, the EETimes/Embedded.com survey found that 50% of developers cite supporting IoT initiatives as “critically important” to “important” in RTOS deployments, along with traditional applications such as consumer electronics and industrial control and automation. At the time of the survey, 15% said they were building AI-driven applications within their RTOS environment.
For example, emerging players within the electric power industry are facilitating the move away from an “antiquated, hardware-dependent power grid to a modern, digital software-based grid,” relates Patrick T. Lee, president and CEO of PXiSE Energy Solutions and vice president of infrastructure and technology at Sempra Energy. The combined use of software and sensors is bringing century-old grid technology into the modern age. A grid project in Western Australia is built on a software-based microgrid controller that monitors grid conditions at the millisecond scale, allowing efficient use of a 1-megawatt solar farm and a 2.5MW battery storage facility. A “software-based controller manages the network’s resources. In the microgrid … solar and wind power, energy storage, and a fossil-fuel power plant supply electricity to homes, factories, and businesses,” says Lee. “The controller continuously balances generation and load within the microgrid and keeps the microgrid’s connection to the main grid stable.”9
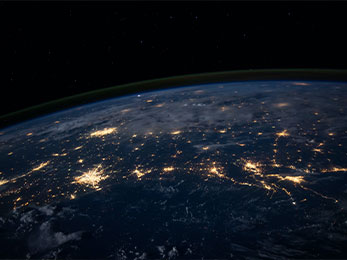
The rise of industrial robots can lead the way to fully automated factories.
Autonomous Systems
RTOSes are paving the way to greater autonomy within machines and systems that power today’s industries. The rise of industrial robots can lead the way to fully automated factories, but they require higher levels of “dexterity and autonomous learning capabilities,” according to a recent analysis by Bastiane Huang. For instance, machine learning “reduces the need for human intervention and enables the robot to handle new parts without the need for engineers to rewrite the program.” In addition, “leveraging AI, the robotic arm can now judge depth more accurately. It can also learn through training and determine if a cup is facing upwards or downwards or is in some other state. Object modeling or visualization can be used to predict and reconstruct 3-D objects.”10
Industrial robots “might require a lot of processing power on the edge. They may be running these intense workloads,” says Pamela Cortez, Azure IoT senior product manager at Microsoft. “Lots of times they might need to run some cloud workload on the edge side on the actual device, which is bringing AI to the device, which will also require beefy devices that can support that. And a lot of these devices, especially modern [ones] — from small devices all the way to those big devices — will probably require some sort of operating system.”11
Such autonomy is also seen within industrial equipment outside the factory. Leading open-pit mining solutions provider Beijing TAGE I-driver Technology Co., Ltd. (TAGE), is developing a cutting-edge software platform for the development of next-generation autonomous mining vehicles, which will not only protect mining workers but also greatly improve the overall economic benefit of mining enterprises. The autonomous haulage system solution is based on an edge-to-cloud architecture, including an intelligent cloud platform, telematics, and an intelligent autonomous mining vehicle. The software platform powering this solution includes an RTOS along with TAGE’s central control unit (CCU) core algorithm module. The CCU in the autonomous vehicle domain controller is responsible for the implementation of core functions of autonomous mining vehicles, such as motion planning, vehicle control, and fault diagnosis. These functions have stringent requirements around the security, safety, and reliability of a system’s operation, as well as for real-time performance and deterministic task execution and switching. They are “paving the way for next-generation mining vehicles,” according to Huang Liming, chief technology officer of TAGE.12
Harvard Business Review